Published in Nature Materials: Ultra-thin piezoelectrics for energy harvesting
Piezoelectric materials can transform mechanical energy into electrical energy and vice versa. Because of that they are used in a multitude of everyday applications from gas lighters to inkjet printers and from ultrasound generators in medical applications (echography devices, blood sensors, lithotripters) to vibration dampers (in cars, skis, helicopter blade).
However, piezoelectric materials have the potential to play an even greater role in society by harvesting the energy that is wasted ubiquitously as vibrations (from cars, house appliances, industrial machine) and transforming it into electricity. But in order to fulfil our dream of paving roads, railways and homes with piezoelectrics, these materials have to be made lighter, thinner and less toxic than the ones available today (which contain heavy chemical elements). An important step into this direction has been achieved by a team led by Beatriz Noheda (Zernike Institute for Advanced Materials) and in collaboration with the Mesa+ Institute of the University of Twente, the CIN2-Barcelona and the CEMES-CNRS Institutes in Toulouse and Zaragoza. The results have been published in Nature Materials.
Flexoelectricity
The researches have shown that ultra-thin films (with thickness of about 100 atomic layers) of piezoelectric materials deposited under carefully designed conditions, self-organize and flex at the nanometer scale in periodic fashion. This produces huge strain gradients (large differences in the distances between atoms) in such a way that a new mechanism to produce piezoelectricity can take place (so-called flexoelectricity). This greatly increases the materials response at these small thicknesses. Moreover, this novel way of producing piezoelectricity is less dependent on the chemical composition and will allow non-toxic and more readily available materials to be investigated for piezoelectric energy harvesting application.
Prof. Beatriz Noheda is Associate Professor of Functional Nanomaterials and Rosalind Franklin Fellow. In 2004 she received a NWO Vidi-grant.
Reference: Flexoelectric rotation of polarization in ferroelectric thin films, G. Catalan, A. Lubk, A. H. G. Vlooswijk, E. Snoeck, C. Magen, A. Janssens, G. Rispens, G. Rijnders, D. H. A. Blank and B. Noheda. Nature Materials.
DOI: http://dx.doi.org/10.1038/NMAT3141
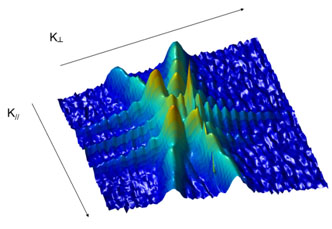
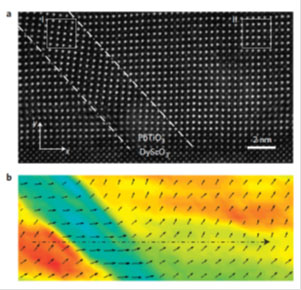
Last modified: | 24 August 2021 09.21 a.m. |
More news
-
17 July 2025
Veni-grants for eleven UG researchers
The Dutch Research Council (NWO) has awarded a Veni grant of up to €320,000 each to eleven researchers of the University of Groningen and the UMCG: Quentin Changeat, Wen Wu, Femke Cnossen, Stacey Copeland, Bart Danon, Gesa Kübek, Hannah Laurens, Adi...
-
14 July 2025
ERC Proof of Concept grant for Kottapalli and Covi
Professors Ajay Kottapalli and Erika Covi have received Proof of Concept grants from the European Research Council (ERC).
-
10 July 2025
Dutch Research Agenda funding for nanomedicine research
Prof Dr Anna Salvati, Dr Christoffer Åberg and Prof Dr Siewert-Jan Marrink have been granted a National Science Agenda (NWA) funding to further develop life-saving drugs based on nanotechnology with the NanoMedNL consortium.