Will it bend or will it break?
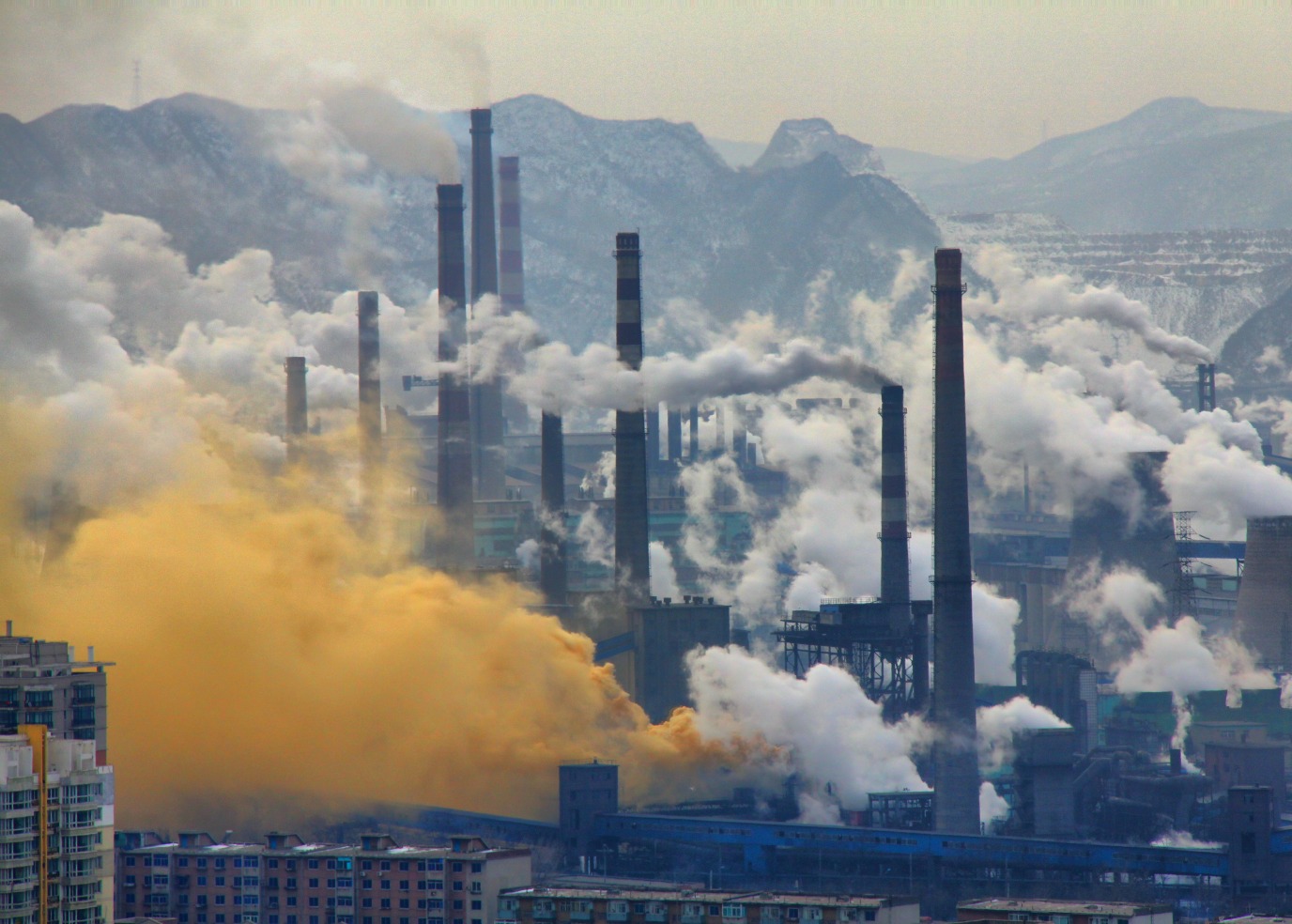
‘The steel industry is facing major changes,’ says Francesco Maresca, a materials scientist at the University of Groningen. ‘We need to reinvent how we produce steel and how we use it.’ Together with Bart Kooi, Yutao Pei, and Jan Post, fellow materials scientists from the University of Groningen, Maresca is involved in the Growing with Green Steel project, which received 124 million euros from the National Growth Fund and another 53 million euros from private investments. The project will be executed by a large consortium of companies and universities, working towards a new, greener life cycle of steel.
FSE Science Newsroom | Charlotte Vlek
In Europe, we produce almost one kilo of new steel per person per day; all this steel goes into daily objects such as keys and paperclips, but also (medical) appliances, cars, and buildings. For years and years, steel was produced by heating iron ore and coke (coal) together. This process extracts oxygen from iron ore, with CO2 as a by-product, making the steel industry one of the largest industrial polluters worldwide.
There is an alternative; using hydrogen (H2) instead of coal would produce water (steam) as a by-product. Better for nature, and better for residents who live near factories. But a different production process will also affect the material properties of this green steel.
Same composition, different material
With the same chemical composition, a material can have different properties, depending on the atomic structure
‘With the same chemical composition, a material can have different properties, depending on the atomic structure,’ Bart Kooi explains. ‘Steel is, in that regard, a complicated material.’ Maresca adds: ‘Compare it to cooking pasta. The same brand of pasta can become gluey or crunchy, depending on how you cook it. It ultimately comes down to the microstructure of the material, how the molecules bond in the process of cooking.’
That’s why the researchers involved in this project will use a powerful combination of experimental, fundamental, and applied research to figure out the best way of ‘cooking’ environmentally friendly steel. This should lead to models that can predict and optimize the material properties of green steel.
(Text continues below photos)
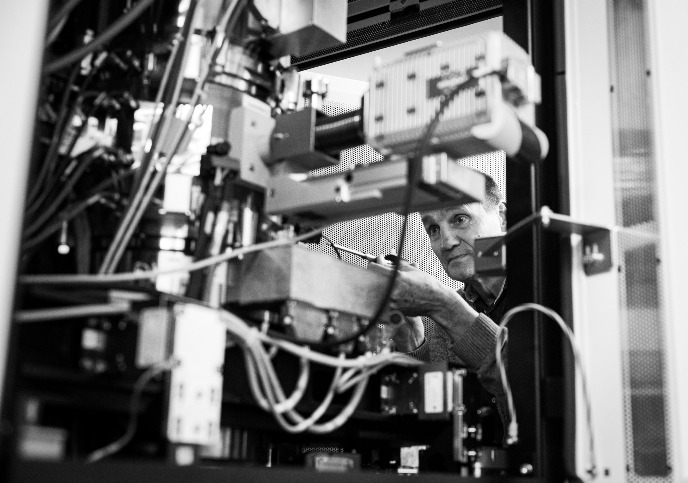
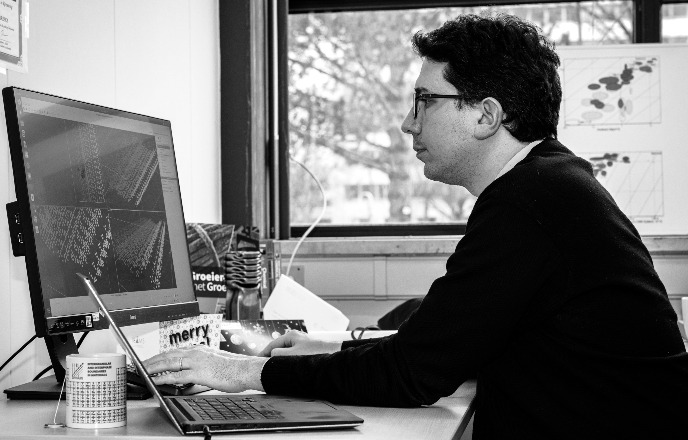
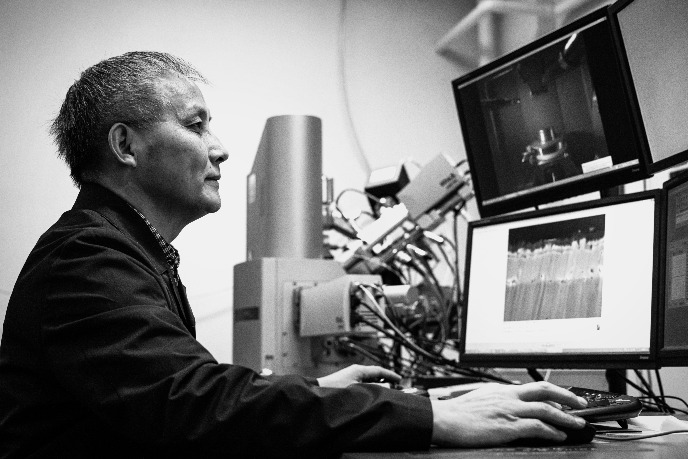
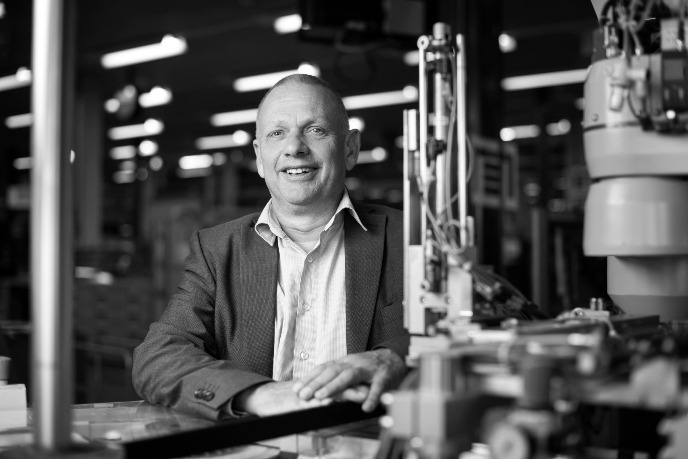
Observing and modelling
The production of the green steel will take place in the laboratories of Tata Steel Netherlands or at Alleima Sweden. Afterwards, the researchers at the UG will get to work. With his electron microscopes, Bart Kooi can look at the atomic structure of the material. Using this information, Francesco Maresca will develop computer models of the material’s microstructure, which in turn will be checked against new observations under the microscope.
Will it bend or break when put under a lot of stress?
Combined, these models and observations can predict what kind of properties the material will have. How strong will it be? How much plasticity will it have? Will it bend or break when put under a lot of stress?
Engineering and predicting
The treatment to make steel corrosion resistant also affects its material properties. Adding a protective coating involves submerging the steel in a hot bath of zinc, thus heating the material. Yutao Pei will work at developing new coatings and coating technology. He will work closely with Bart Kooi and Francesco Maresca, who will keep checking whether the coatings preserve the steel’s desired microstructure.
Jan Post, working at the University of Groningen and at Philips Drachten, is responsible for the user-phase of the entire consortium. Together with other institutions and private companies, he will develop predictive models for specific applications, building on the observations and computer models of Kooi and Maresca. Posts’s models will help to predict how a razor made out of a new type of green steel will keep after intensive use, or a car. Or how long steel bearings of a wind turbine will last, or a landing gear of an airplane.
Although diamond and graphite both consist of pure carbon, they have very different properties. That’s due to the microstructure of the materials: in diamond, the carbon atoms are arranged in a 3D network, making the material very strong. So much so, that you can use it to drill into concrete. On the other hand, graphite is organized in 2D planes that can easily slide over each other, making it suitable as a lubricant.
‘By using certain temperature treatments, such as heating and subsequent rapid cooling, we can influence the structure of a material,’ Bart Kooi explains. This process is already used to produce strong aluminium. Kooi: ‘Steel is and remains one of the most complex materials when it comes to such heat treatments, still leaving ample room for optimization.’
His transmission electron microscope reveals the atomic structure of a sample by shooting a beam of electrons through the material. The way the electrons in the beam change course reveals the positions of the atoms. Kooi adds: ‘A nice thing about the various electron microscopes we have is that we can analyse the microstructure on all kinds of length scales from a millimetre scale down to the atomic scale, 10 million times smaller than a millimetre. Once you know this microstructure, you can determine the material properties and you’ll know what applications the steel is suitable for.’
The microscope produces an image of the material, while with a computer model you can also make predictions and check what the effect will be if you were to adapt the production process.
Francesco Maresca will develop computer models of the microstructures of green steels. Maresca: ‘Using these models, we can predict the engineering properties, such as strength, hardness, sensitivity to corrosion, and durability. We incorporate this information into the production process to optimize it in such a way that we obtain the best properties.’
To make steel corrosion resistant, steel strips are submerged in a large bath of liquid zinc. The zinc adheres to the surface of the steel strips and forms a thin coating that prevents rust. This process takes place at high temperatures, at around 460 degrees Celsius. ‘All of this will affect the microstructure of steel,’ Yutao Pei explains.
In his research, Pei will develop new coatings and energy-saving coating technology for green steel. He is currently working with coatings for other applications that are applied using vapour instead of liquids. Using that method, the steel itself can be kept at a lower temperature. When developing his coatings, Pei will also consider the full life cycle of steel: for instance, by having a coating that can easily be removed for recycling.
‘If you want to establish through experiments how long steel bearings, or a car, or a razor will last, you easily need ten or more years,’ Jan Post explains. You would have to build a handful of wind turbines and observe them for fifteen years. Alternatively, you could make a predictive computer model of of a product in which you consider the material properties of the steel: a digital twin.
Based on Maresca’s computer models, Jan Post will develop such digital twins for various applications and manufacturing processes from stainless steel. Post: ‘In the past, you would test things out in a factory, but now all is done using digital twins. That makes a huge difference, since you don’t have to adjust the production process at a later phase. We’ve made process models at Philips and at the University of Groningen that can shorten the development time of new Philips products and processes from ten to just a few years.’
Last modified: | 15 February 2024 10.21 a.m. |
More news
-
29 April 2024
Tactile sensors
Every two weeks, UG Makers puts the spotlight on a researcher who has created something tangible, ranging from homemade measuring equipment for academic research to small or larger products that can change our daily lives. That is how UG...
-
16 April 2024
UG signs Barcelona Declaration on Open Research Information
In a significant stride toward advancing responsible research assessment and open science, the University of Groningen has officially signed the Barcelona Declaration on Open Research Information.
-
02 April 2024
Flying on wood dust
Every two weeks, UG Makers puts the spotlight on a researcher who has created something tangible, ranging from homemade measuring equipment for academic research to small or larger products that can change our daily lives. That is how UG...